
Wideo: „Cuda” technologii Piotra Wielkiego lub za kogo bije dzwon
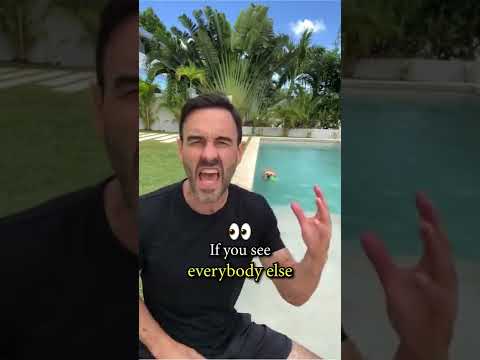
2024 Autor: Seth Attwood | [email protected]. Ostatnio zmodyfikowany: 2023-12-16 16:14
Artykuł mojego współpracownika.
„Jeśli fakty są sprzeczne z teorią, musisz odrzucić teorię, a nie fakty”.
A. Skjarow
Nikt nie pozostaje obojętny, a wspaniałe kamienne wazony Ermitażu na zawsze podbiją swoim pięknem i fantastycznym wykonaniem. Jaspis, granit, malachit – różnorodność materiałów i kolorów robi wrażenie. A solidne wymiary wazonów, niezwykle skomplikowane elementy i perfekcyjne wypolerowanie powierzchni budzą wiele pytań o ówczesne technologie. Przejdźmy z hal Ermitażu do warsztatów produkcyjnych i zobaczmy, jak przy dość wąskiej gamie materiałów produkcyjnych i rozwiązań technicznych można było wykonać tak doskonałe produkty.

W tym celu specjalnie poszedłem do Ermitażu. Jeszcze raz dokładnie obejrzałem eksponaty, a także znalazłem szyldy o „producentu”. Tak jest napisane: „Jekaterynburska Fabryka Lapidarzy”. Zatrzymać! Co ma z tym wspólnego cięcie?
Granil to (z włoskiego graniglia - okruchy, granulki) ogólna nazwa szklanek o specjalnym składzie zmiażdżonym do określonej wielkości. Faseta służy do zdobienia płytek ceramicznych, granitu ceramicznego. Przechowywanie może być błyszczące lub matowe, przezroczyste, przyciemnione, białe lub kolorowe, z efektami żyrandolowymi lub metalicznymi itp. Mogą służyć zarówno do stworzenia efektu wizualnego, jak i nadania określonych właściwości. Co ma z tym wspólnego szkło? Porozmawiam o tym później, w innym artykule. A oficjalna historia mówi, że cięcie i fasetowanie to te same podstawowe słowa. A nawet więcej – mają to samo znaczenie! Niech tak będzie, studiowali to również w specjalnych instytucjach, wśród nich są lekarze i profesorowie nauk historycznych i innych. A my jesteśmy prostymi ludźmi. Więc dalej. Okazuje się, że w tym czasie istniały trzy zakłady cięcia i szlifowania.
W Jekaterynburgu, w Kolyvan na Ałtaju iw Peterhofie pod Petersburgiem. O tych fabrykach można przeczytać w Internecie. Szlifierki napędzane były przez młyny wodne. Nie znalazłem żadnych informacji o ściernicach. Z czego i jak powstały ścierniwa do polerowania tak twardych materiałów, nie wiemy. Ale zrobili zarówno kolumny, jak i wazony! Więc zrobiliśmy też materiały ścierne. Zaskakujące jest jednak to, że w takich branżach potrzeba wielu takich materiałów eksploatacyjnych o różnej wielkości ziarna. A do tego z kolei potrzebna jest osobna znaczna produkcja i własność technologii. W końcu materiały ścierne (te, którymi szlifują i polerują) muszą być twardsze. A ich przetwarzanie nie jest łatwym zadaniem. I nigdzie o tym nie ma wzmianki. Na to też zamknijmy oczy. Po rewolucji 1917 r. fabryki w Kolyvan i Jekaterynburgu zaprzestały produkcji, pozostały tylko fabryki Peterhof, które po 1947 r. zostały znacznie zmodernizowane. Jeszcze bardziej poprawnie zbudowano nowy! Woda była dostarczana żeliwną rurą, były 2 turbiny o mocy 15 koni mechanicznych każda i tak dalej. Jak wcześniej wyglądała produkcja? Aby to zrobić, musisz odwiedzić muzeum w fabryce Kolyvan. Jest tam nawet fałszywy młynek! Rozważymy ten układ.

Więc to jest protoplasta tokarki! W ten sposób oficjalna historia tłumaczy powstanie kolumn do soboru Chrystusa Zbawiciela w Moskwie, a nawet do soboru św. Izaaka! Wszystko jest łatwe i proste! Młyn wodny obraca koła zębate, one napędzają wał napędem pasowym, a to z kolei oś przodka tokarki. Ale obliczenia inżynieryjne przynoszą własną muchę w tej słodkiej beczce miodu. Kolumny do katedry Chrystusa Zbawiciela miały ponad trzy metry długości, a jeszcze więcej do katedry św. Izaaka. A przy obliczaniu masy półfabrykatów pojawia się problem - każdy półfabrykat ma co najmniej więcej niż 2 tony.
Szablon jest już zainstalowany w modelu. Jak drewniana oś trzyma tak ciężki blok kamienia? Na nowoczesnych tokarkach do mocowania części (uchwytu) stosuje się bardzo mocne urządzenie, które nie tylko ściska obrabiany przedmiot na końcach, ale także zaciska go „palcami” jak ośmiornica!

Uchwyt tokarski

Zaciśnięta część A w modelu jest po prostu mocowana z obu stron za pomocą drewnianej osi. Nie sprzeczajmy się, to tylko układ, przymknijmy na to oczy. Przymknijmy oczy na to, że jedna z osi mocujących powinna poruszać się poziomo. Jak najpierw „odjechać”, a po zamontowaniu przedmiotu obrabianego „dokręcić” go.

A na modelu pokazano nam sztywną, już z częścią stałą, szlifierkę. Nie doszukujmy się w ten sam sposób wady średnicy osi. Kiedyś były inne drzewa, silne. Niech Bóg im błogosławi za te błędy. Ale to, czego nie wybacza odporność na materiały i inżynierię, to błędna kalkulacja tarcia. W takim przypadku napęd pasowy musi obracać obrabiany przedmiot ważący 2 tony lub więcej! A wszystko kosztem młyna wodnego. Bez uwzględnienia, że powierzchnie drewniane będą same szlifować taśmą, i tak już niska wydajność spadnie jeszcze bardziej. Ale można założyć, że w razie potrzeby wał i paski zostały wymienione na czas. Ale głównym błędem tego układu (a w konsekwencji całej proponowanej technologii) są osie, na których obracał się przedmiot obrabiany! Pod ciężarem obrabianego przedmiotu, w punktach obrotu osi, tarcie jest tak duże, że potrzebne są tytaniczne wysiłki, aby je obrócić.
Jeśli dla ułatwienia momentu obrotowego zrobimy szczelinę między osią a pionową kolumną, to oś przestanie przytrzymywać obrabiany przedmiot i wypadnie. A jeśli zmusimy go do obracania się, obciążenie na drewnianych osiach będzie działać przez niewielką ilość czasu (według wstępnych szacunków nie dłużej niż 10 minut). Wynika z tego, że ten młynek nie mógł działać. I dlatego na tej szlifierce nie wykonano kolumn do wszystkich tych katedr.

Spójrzmy teraz na inny młynek. Z dużego wału napęd pasowy obracał małe wałki zamocowane w zawieszonych drewnianych wahadłach i przekazywał moment obrotowy na ściernicę. Czy wszystko znów jest łatwe i proste? Nie! Aby przenieść rotację, pas musi być zawsze napięty. A potem okazuje się, że szlifować możemy tylko na odległość napiętego paska. Ponadto jesteśmy zobowiązani do zapewnienia napięcia pasa rękami. Jednocześnie upewnij się, że ściernica jest dociśnięta do przedmiotu obrabianego. Prędkość obrotowa młyna wodnego wynosiła średnio od 60 do 150 obr/min! Współczesny instrument to około 1000.
Nie znajduję nawet wady w sposobie przeniesienia obrotu na drugą ściernicę (którą figurka trzyma w czerwonej koszulce) - nie pokazano schematu obrotu paska o 90 stopni (a to wymaga specjalnego urządzenia, ale co prowadzi do dodatkowej utraty wydajności). Przynajmniej za pomocą tego urządzenia możesz szlifować. Ale tylko w linii prostej. I ciągle przesuwając obrabiany przedmiot tam iz powrotem. A proces polerowania obejmuje co najmniej 10 kolejnych przejść z różnymi rozmiarami ziarna ściernego! Teraz pytanie! Jak wypolerować wazon? Skręcać, obracać i przechylać? Czyli okazuje się, że produkty, czasami sięgające kilku ton, poruszały się w przestrzeni tak, jak chciał mistrz? Dlatego ten młynek nie mógł polerować wazonów z Ermitażu! Wstępne obliczenia przeprowadzono przy użyciu specjalnych programów inżynierskich. Programy te służą do tworzenia nowoczesnych mechanizmów high-tech. Wszystkie symulowane zastosowania tych młynków dały negatywne odpowiedzi. Ponadto przy badaniu mechanizmu tych szlifierek nie uwzględniono wielu niedociągnięć (i zawsze na korzyść oficjalnej historii!). A niektóre z nich, jak np. brak produkcji materiałów ściernych, twardość niektórych obrabianych materiałów jest zbliżona do twardości granitu (a to już bardzo duży problem!), technologiczna niemożność polerowania i szlifowania skomplikowanych elementów wazonów (wypukłe krawędzie, rowki, płatki) generalnie sprowadza się do braku możliwości zastosowania tej technologii w tym zakresie. Tę technologię można śmiało nazwać „bajką Munchausena”. Zwiedzający muzea nie obeznani w szczegółach technicznych z zapomnieniem słuchają barwnych opowieści przewodników.
Łatwiej jest uwierzyć, że „zrobiło się z łatwością” i po cichu przejść do następnego eksponatu, niż protestować i bać się ukradkowych spojrzeń i rozmów, na przykład jak śmiesz się kłócić – wszyscy wierzą, a ty jesteś tu taki mądry? Oto, jak mówią nam o dostawie 19-tonowej carskiej wazy z wazy szlifierskiej Kolyvan do Petersburga: „19 lutego 1843 r. Pociąg koni zaprzężonych w specjalne sanie (od 154 do 180, w zależności w terenie) zabrał miskę z Kolyvan do Barnauł, a następnie do molo Utkinskaya nad rzeką Chusovaya. Szczegółowo załadowaliśmy miskę na tratwy i skierowaliśmy się wzdłuż rzeki Czusowaja do rzeki Kamy, od rzeki Kamy do rzeki Wołgi, wzdłuż rzeki Wołgi z holownikami, a następnie wzdłuż kanału obejściowego do rzeki Newy”. Najpierw zrobili specjalne sanie (stracili czas, wysiłek, materiały) i ciągnęli w zaprzęgu 150-180 koni. Przy tak wielu koniach mamy problem z synchronicznością. A potem, po przybyciu nad rzekę, miskę rozebrano na części składowe i rozebrano na tratwach.
Gdzie jest logika??? Toczymy kwadratową, nosimy okrągłą. Dlaczego nawet jako dzieci wątpiliśmy w prawdziwość opowieści barona Munchausena i dorastając wierzymy w takie bzdury? Jeśli wazon był składany, po co zrywać monolit o wadze ponad 30 ton, przeciągać go po górach i wąwozach, a następnie robić nie solidny wazon, ale z części? „Prace rozpoczęły się w lutym 1828 roku. Przy pomocy 230 robotników kamień został wyciągnięty do murowanej szopy i podniesiony na wysokość jednego metra. Około 100 rzemieślników zajmowało się pierwotną obróbką monolitu, po czym w 1830 r. Kamień został położony na kłody i ręcznie, przy pomocy 567 osób, przeniósł blok 30 wiorst do Kolyvan”. 567 osób przeciągnęło monolit, by później, już w fabryce, rozwalić go na kawałki. PIĘĆset sześćdziesiąt siedem osób !!! Przeciągnęli bryłę. STO OSIEMDZIESIĄT KONI !!! Zaciągnęli wazon. Jak to brzmi ?! Wiarygodny! A potem, po takich staraniach, zostały rozebrane na części i załadowane na tratwy…
To wszystko. Całe zdrowie i jasny umysł!
Zalecana:
25 głównych tajemnic rosyjskiej historii sprzed Piotra

Churchill skarżył się, że nie jest w stanie przewidzieć działań Rosji, ponieważ „Rosja jest zagadką owianą tajemnicą, umieszczoną w puzzlach”. Ten cytat z brytyjskiego polityka byłby najlepszym epigrafem do podręcznika historii Rosji. Przedstawiamy naszą wersję 25 głównych tajemnic historii Rosji z czasów przed Piotrem
Wódka, kąpiel i czosnek. Jak traktowano Słowian w epoce Piotra Wielkiego

W XVII wieku zatłoczone życie w Rosji toczyło się tylko w klasztorach i miastach: Moskwę porównywano wielkością z Paryżem i Londynem. Naturalnie świat wokół ówczesnych mieszczan wydawał się pełen niebezpieczeństw - wciąż nie było kanalizacji, wodociągów i wystarczającej liczby lekarzy, a ziemię niemal co roku odwiedzały nieurodzaje, pożary, choroby
Londyn nie zwraca złota Wenezueli – dzwon dla Rosji?

Ta międzypaństwowa nieuprzejmość została zademonstrowana przez Wielką Brytanię w stosunku do Wenezueli. Londyn pod śmiesznym pretekstem odmawia Caracasowi wenezuelskiego złota, które jest przechowywane na jego terytorium. Paradoksalnie to, co się dzieje, jest bezpośrednio związane z Rosją
Amarant jest głową lub wrogiem Piotra Wielkiego

Słowo AMARANT. Mara jest boginią śmierci, a przedrostek „A” oznacza negację w języku - na przykład moralno-niemoralny itp. Okazuje się więc, że AMARANT dosłownie oznacza ten, który zaprzecza śmierci, a raczej ten, który daje nieśmiertelność
Dla kogo i dla kogo przydatne są rozbłyski słoneczne?

Media tworzą katastrofę z każdej epidemii, sieją panikę. Czyli ta opinia publiczna o Słońcu jest korzystna dla właścicieli mediów?